Our Deep Cryogenic Treatment Process
Take Five Audio feels strongly about the benefits of deep cryogenic processing and has made the investment in equipment, time, and necessary safety procedures to make these benefits available to our customers. Our proprietary processing profiles along with tight quality control and state of the art equipment result in the highest quality cryo treated audio parts available.
We perform all deep cryogenic processing in house using our custom built Cryotron processor. The need for a true deep cycle as well as tight control of all phases of the cryogenic process has led us to make the substantial investment in a custom built cryo chamber designed specifically for our needs. Having our own cryogenic processor allows us the flexibility to experiment and develop the optimal treatment cycles for the various audio related parts and cable we sell.
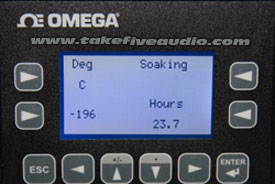
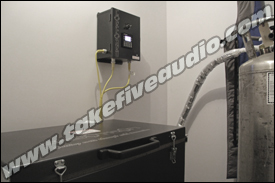
Not all audio parts and cable respond in the same way to cryogenic treatment. For this reason experimentation is essential in order to develop the optimum treatment cycle for audio parts that vary widely in construction and materials such as cables and vacuum tubes. The experimentation required to find the optimum profiles is not possible or prohibitively expensive if you are working with an outside supplier.
We perform cryogenic processing on a regular weekly basis. Having our own processor on-site allows us to quickly turn around parts since we are cycling loads constantly. Our weekly processing schedule means parts received by Monday will ship back to the customer on the following Monday.
Working with LN2 requires costly specialized equipment, as well as extreme care. A deep cryogenic treatment cycle is a painstaking process that will take several days to complete depending on the length of the ramp down and soak time that was selected for the load. The treatment cycle consists of three distinct phases:
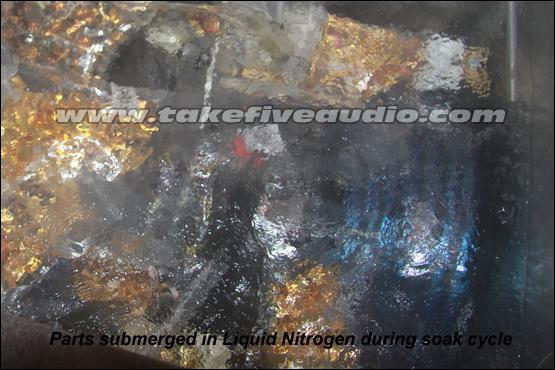
Ramp Down
In the ramp down cycle the parts are very slowly cooled using Nitrogen vapor. This phase will take 8 to 12 hours depending on the profile and items being treated. The computer controlled processor lowers the temperature in the chamber slowly to avoid thermal shock. During this pre treatment cycle the temperature inside the chamber reaches about -280 F before the liquid Nitrogen begins to condense and fill the chamber, this is about as low as any vapour processor can get using a "dry" process. When the liquid nitrogen is introduced at these low temperatures there is no risk of thermal shock.
Soak
As the ramp down cycle completes the chamber becomes filled with the condensed LN2 and the soak cycle begins. During the soak cycle the machine is maintaining liquid level in the chamber ensuring the parts remain fully submerged LN2 at a constant -195.78 C.
When the soak cycle completes the parts do not immediately begin to ramp up in temperature since they will remain totally submerged for several more hours.
Return to Ambient
The processor uses approximately 320 liters of LN2 to complete the ramp down and soak cycles. When the processor completes the soak cycle the LN2 is stopped and the liquid Nitrogen in the chamber is allowed to boil off. The return to ambient temperature is a slow process which takes two days, during which time it is constantly monitored by the processor. When the temperature inside the chamber is within a few degrees of ambient the processor is opened and the parts are removed.
All phases of the treatment process are carefully controlled by computer to avoid damage from thermal shock, frost and condensation. The greatest risk of damage is from thermal shock which results when the cable or parts have the temperature dropped or raised too quickly. This is not a concern with our computer controlled chamber.
In the event of a power failure it is possible that the contents of the cryogenic processor could be damaged due to temperature fluctuations. For this reason our processor is on an uninterruptible power supply (UPS) which is further backed by an automatic emergency generator, guaranteeing that once started our process cycle goes to completion.
How does it work?
Cryogenic Processing of metal at temperatures at or below -195 C causes molecular changes to occur. As metal objects cool, they shrink. With the -195 C temperature and shrinkage that results from LN2 immersion, the crystal boundaries of metal conductors align more closely with one another increasing conductivity and reducing noise. The tightened grain structure stays intact through the slow warming process and is stable at room temperature and in the case of vacuum tubes, remains stable at operating temperature. The change is permanent.
How does that benefit audio?
Different metals used in audio connectors and cable respond differently to cryogenic processing. Generally speaking we have found that the lower the initial quality of the treated part, lets say OFC compared to OCC, the greater the perceived improvement. Cryogenic processing has improved the performance of most all the audio related items we have experimented with.
The most commonly noted improvements are:
Not all Cryogenic Processing is Created Equal
Some of our competitors are using short ramp down times along with short soak cycles of 10 hours in a vapor processor and claiming "Deep Cryo Treatment". A short generic vapour cycle does not take into account things like material thickness/density, the type of material being processed, or the amount of material in the processor during the cycle. Any one of these variables can prevent the materials from reaching the desired core temperature of -195 C, in fact, a vapour process will never reach this temperature.
If -195 C is not reached during ramp down and maintained during the soak cycle complete material transformation does not occur. Our processor floods the chamber with liquid Nitrogen after the ramp down is complete covering the parts completely and maintains total submersion throughout the soak cycle and a portion of the ramp up cycle. This ensures that all the parts in the entire load reach the ideal -195 C core temperature for the required amount of time ensuring that maximum benefits are realized.
Log printout
Our cryogenic process is a true Deep Cryo process that maintains a soak temperature of -195 C for 24 hours or more. Our processor uses a digital controller and log recorder, we supply a graph printout that displays the time and temperatures that your materials have seen from start to finish with every custom job. Anyone doing deep cryo treating can supply you with a chart that shows the time and temperatures used, be sure to ask for a copy. Below is a printout of the ramp down/soak log of a recent load.
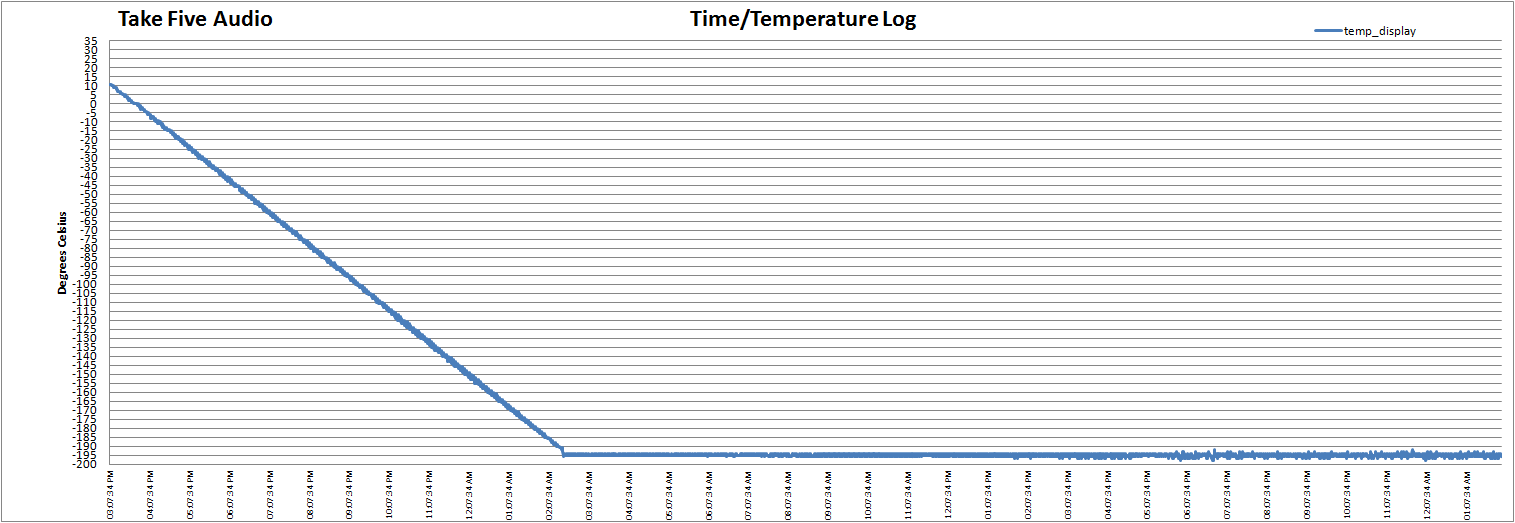
Is it safe?
We have treated thousands of audio parts, miles of wire and cable and seldom experience a problem, but please realize that anything going through deep cryogenic treatment is in danger of sustaining damage. We do however take all precautions to ensure the risks are minimized. Your items are never handled while at extreme low temperatures. We also use special containers for tubes to keep them from moving in the chamber. We treat your precious audio equipment with the utmost care and respect in a safe and clean environment.
Click This Link For More Info and Pricing
We perform all deep cryogenic processing in house using our custom built Cryotron processor. The need for a true deep cycle as well as tight control of all phases of the cryogenic process has led us to make the substantial investment in a custom built cryo chamber designed specifically for our needs. Having our own cryogenic processor allows us the flexibility to experiment and develop the optimal treatment cycles for the various audio related parts and cable we sell.
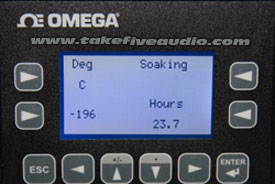
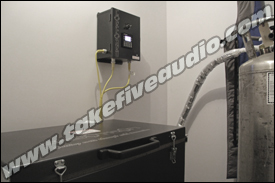
Not all audio parts and cable respond in the same way to cryogenic treatment. For this reason experimentation is essential in order to develop the optimum treatment cycle for audio parts that vary widely in construction and materials such as cables and vacuum tubes. The experimentation required to find the optimum profiles is not possible or prohibitively expensive if you are working with an outside supplier.
We perform cryogenic processing on a regular weekly basis. Having our own processor on-site allows us to quickly turn around parts since we are cycling loads constantly. Our weekly processing schedule means parts received by Monday will ship back to the customer on the following Monday.
Working with LN2 requires costly specialized equipment, as well as extreme care. A deep cryogenic treatment cycle is a painstaking process that will take several days to complete depending on the length of the ramp down and soak time that was selected for the load. The treatment cycle consists of three distinct phases:
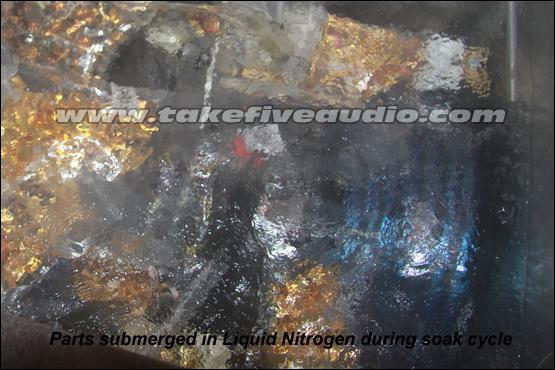
In the ramp down cycle the parts are very slowly cooled using Nitrogen vapor. This phase will take 8 to 12 hours depending on the profile and items being treated. The computer controlled processor lowers the temperature in the chamber slowly to avoid thermal shock. During this pre treatment cycle the temperature inside the chamber reaches about -280 F before the liquid Nitrogen begins to condense and fill the chamber, this is about as low as any vapour processor can get using a "dry" process. When the liquid nitrogen is introduced at these low temperatures there is no risk of thermal shock.
Soak
As the ramp down cycle completes the chamber becomes filled with the condensed LN2 and the soak cycle begins. During the soak cycle the machine is maintaining liquid level in the chamber ensuring the parts remain fully submerged LN2 at a constant -195.78 C.
When the soak cycle completes the parts do not immediately begin to ramp up in temperature since they will remain totally submerged for several more hours.
Return to Ambient
The processor uses approximately 320 liters of LN2 to complete the ramp down and soak cycles. When the processor completes the soak cycle the LN2 is stopped and the liquid Nitrogen in the chamber is allowed to boil off. The return to ambient temperature is a slow process which takes two days, during which time it is constantly monitored by the processor. When the temperature inside the chamber is within a few degrees of ambient the processor is opened and the parts are removed.
All phases of the treatment process are carefully controlled by computer to avoid damage from thermal shock, frost and condensation. The greatest risk of damage is from thermal shock which results when the cable or parts have the temperature dropped or raised too quickly. This is not a concern with our computer controlled chamber.
In the event of a power failure it is possible that the contents of the cryogenic processor could be damaged due to temperature fluctuations. For this reason our processor is on an uninterruptible power supply (UPS) which is further backed by an automatic emergency generator, guaranteeing that once started our process cycle goes to completion.
How does it work?
Cryogenic Processing of metal at temperatures at or below -195 C causes molecular changes to occur. As metal objects cool, they shrink. With the -195 C temperature and shrinkage that results from LN2 immersion, the crystal boundaries of metal conductors align more closely with one another increasing conductivity and reducing noise. The tightened grain structure stays intact through the slow warming process and is stable at room temperature and in the case of vacuum tubes, remains stable at operating temperature. The change is permanent.
How does that benefit audio?
Different metals used in audio connectors and cable respond differently to cryogenic processing. Generally speaking we have found that the lower the initial quality of the treated part, lets say OFC compared to OCC, the greater the perceived improvement. Cryogenic processing has improved the performance of most all the audio related items we have experimented with.
The most commonly noted improvements are:
- Deeper, wider, more three dimensional soundstage
- More articulate bass reproduction
- Smoother, more refined high frequency response
- Improved dynamic range
- Lower noise floor
Not all Cryogenic Processing is Created Equal
Some of our competitors are using short ramp down times along with short soak cycles of 10 hours in a vapor processor and claiming "Deep Cryo Treatment". A short generic vapour cycle does not take into account things like material thickness/density, the type of material being processed, or the amount of material in the processor during the cycle. Any one of these variables can prevent the materials from reaching the desired core temperature of -195 C, in fact, a vapour process will never reach this temperature.
If -195 C is not reached during ramp down and maintained during the soak cycle complete material transformation does not occur. Our processor floods the chamber with liquid Nitrogen after the ramp down is complete covering the parts completely and maintains total submersion throughout the soak cycle and a portion of the ramp up cycle. This ensures that all the parts in the entire load reach the ideal -195 C core temperature for the required amount of time ensuring that maximum benefits are realized.
Log printout
Our cryogenic process is a true Deep Cryo process that maintains a soak temperature of -195 C for 24 hours or more. Our processor uses a digital controller and log recorder, we supply a graph printout that displays the time and temperatures that your materials have seen from start to finish with every custom job. Anyone doing deep cryo treating can supply you with a chart that shows the time and temperatures used, be sure to ask for a copy. Below is a printout of the ramp down/soak log of a recent load.
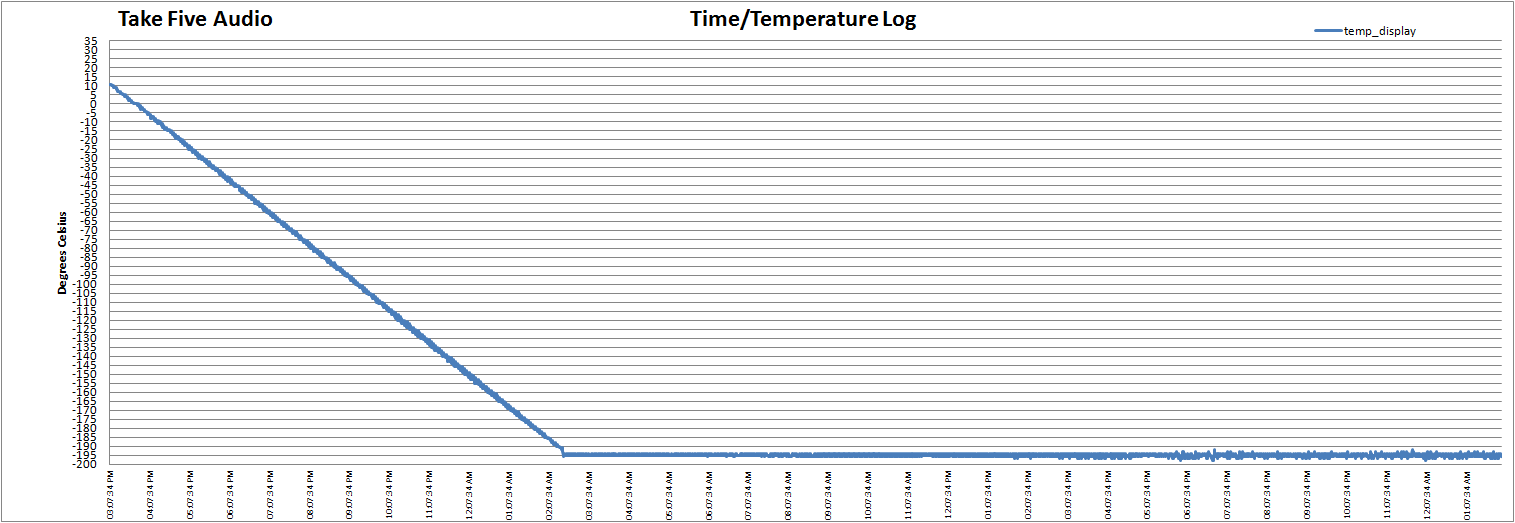
Is it safe?
We have treated thousands of audio parts, miles of wire and cable and seldom experience a problem, but please realize that anything going through deep cryogenic treatment is in danger of sustaining damage. We do however take all precautions to ensure the risks are minimized. Your items are never handled while at extreme low temperatures. We also use special containers for tubes to keep them from moving in the chamber. We treat your precious audio equipment with the utmost care and respect in a safe and clean environment.
Click This Link For More Info and Pricing